Oil cylinder is a common industrial equipment, which is mainly used to store and transport liquid or gas.
In order to ensure the safety and normal operation of the oil cylinder, the commissioning test is an important link that cannot be ignored.
Here is Oil cylinder manufacturer Some common oil cylinder debugging and testing methods.
1、 Static test
Static test is mainly to test the structure, sealing and pressure resistance of the oil cylinder.
Specific test steps include:
1. Conduct visual inspection on the oil cylinder, including checking whether the welded joints, valves, threads, etc. of the oil cylinder are intact, and eliminate various surface defects.
2. Use water or air for pressure test to test the tightness and pressure resistance of the oil cylinder.
3. The pressure should be gradually increased to ensure that the cylinder can withstand the pressure required by the design.
4. For the whole water test, it is necessary to fill the oil cylinder to the design water level to check whether there is water leakage.
5. For the whole air test, it is necessary to fill the compressed air and check whether there is air leakage.
2、 Dynamic test
Dynamic test is mainly used to test the performance of oil cylinder during operation.
Specific test steps include:
1. Open the inlet and outlet valves of the oil cylinder and fill the designed working medium.
2. Conduct operation test on the oil cylinder, observe the working state and operating parameters of the oil cylinder, and record them, including pressure, temperature, flow, liquid level and other parameters.
3. By monitoring and analyzing these parameters, the normal working condition of the oil cylinder can be ensured.
4. Carry out load test, add a predetermined working load to the oil cylinder, and observe whether the performance of the oil cylinder meets the design requirements.
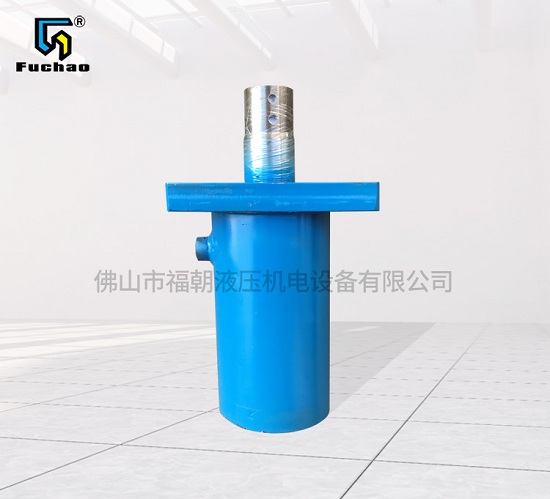
3、 Temperature test
Temperature has an important influence on the operation stability and life of oil cylinder.
In testing, we need to:
1. Temperature monitoring shall be carried out at different positions of the oil cylinder to determine the hot spot and cooling point of the oil cylinder and ensure that the oil cylinder operates within the designed operating temperature range.
2. Simulate the ambient temperature change, observe the temperature change of the oil cylinder, and analyze its impact.
4、 Control system test
The control system is an important part of the oil cylinder, which is used to control the start and stop, operation, maintenance and other aspects of the oil cylinder.
In the test, you need to:
1. Check whether the appearance and wiring of the control system are correct. Check whether the switch, valve and other components work normally and ensure the reliability of electrical connection.
2. Carry out function test, start and stop the oil cylinder through the control system, set the running time, and conduct automatic fault diagnosis to ensure the normal and reliable function of the control system.
5、 Safety test
Safety is critical to the operation of the cylinder.
In testing, we need to:
1. Check and test the safety valve and protective device of the oil cylinder to ensure that the pressure can be released in time when the pressure exceeds the design range to prevent the oil cylinder from cracking.
2. Check the explosion-proof performance of the oil cylinder, and test whether the oil cylinder can withstand the predetermined bursting pressure to avoid explosion or leakage accidents.
Oil cylinder commissioning test is an important link to ensure the safe and normal operation of oil cylinder. Through static test, dynamic test, temperature test, control system test and safety test, the performance of oil cylinder can be comprehensively evaluated, potential problems can be found, and corresponding measures can be taken to repair and optimize. At the same time, safety shall be paid attention to during the test, and the operation shall be carried out in strict accordance with relevant standards and specifications to ensure the accuracy and reliability of the test.