Oil cylinder is a device used to store and transport liquid, which is widely used in industrial production and other fields.
The selection and commissioning of oil cylinder is an important link to ensure its normal operation and safe use.
The following will give you a detailed introduction Oil cylinder manufacturer Precautions during model selection and commissioning.
1、 The selection of oil cylinder is determined according to the use demand and working environment conditions, and the following factors should be considered generally:
1. Capacity and size:
Select appropriate cylinder capacity and size according to the amount of liquid stored and site conditions.
Too small capacity will lead to insufficient storage, and too large capacity will waste space.
2. Material and pressure rating:
According to the liquid characteristics and working pressure requirements, select the appropriate cylinder material and pressure level.
Common materials include carbon steel, stainless steel, etc. The pressure grade is mainly determined according to the working pressure.
3. Sealing and safety:
Considering the sealing and safety requirements of the oil cylinder, select the corresponding sealing structure and safety device, such as safety valve, bursting disc, etc.
Ensure that no safety accidents such as leakage or explosion occur during the operation of the oil cylinder.
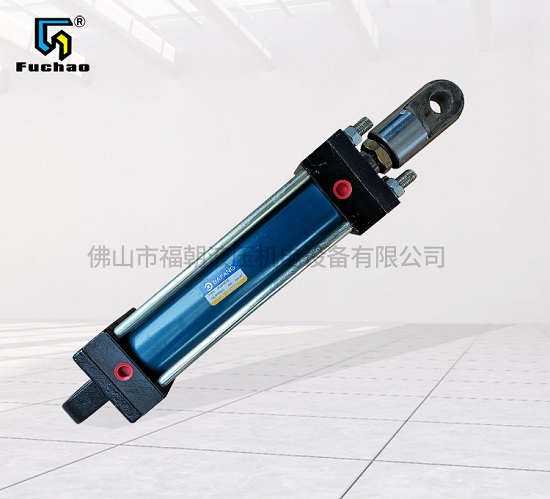
2、 In the process of model selection, the oil cylinder manufacturer needs to understand the specific needs and working scenarios of users,
Provide appropriate solutions, taking into account such factors as economy and reliability.
After selecting the appropriate cylinder model and specification, commissioning is also required.
The commissioning of oil cylinder is to ensure its normal operation before use, and the specific steps are as follows:
1. Check the oil cylinder:
Check whether the appearance of the oil cylinder is intact, whether each connection part is firm, and whether there is oil leakage. If any problem is found, repair or replace the corresponding accessories in time.
2. Cleaning and handling:
Clean the impurities and dirt inside and outside the oil cylinder to ensure that its surface is smooth and clean without pollution. Rust removal, spraying and insulation treatment can be carried out as required.
3. Installation and fixation:
According to the work demand and site conditions, select the appropriate installation position and fixing method to ensure the stability and reliability of the oil cylinder.
During installation, sufficient operation space shall be reserved, and manholes and drainage holes shall be reserved.
4. Sealing and connection:
Check the sealing performance of the oil cylinder to ensure that there is no leakage at each connection part. If leakage is found, seal it in time.
5. Stress test:
Use pressure gauge and other tools to pressure test the oil cylinder to ensure that it can withstand the design working pressure.
During the test, the pressure can be gradually increased to check the response and deformation of the cylinder.
6. Corrosion protection and insulation:
Corresponding anti-corrosion and insulation measures shall be taken according to the service environment and liquid characteristics to extend the service life of the oil cylinder.
7. Identification and record:
The oil cylinder shall be identified and recorded, including model, specification, installation date, maintenance record, etc., to facilitate future management and maintenance.
The above is the general steps for the oil cylinder manufacturer to select and debug. The specific operation process and precautions need to be adjusted according to the actual situation. During the whole selection and commissioning process, the oil cylinder manufacturer shall follow relevant standards and safety specifications to ensure the reliability and safety of the oil cylinder. At the same time, it is suggested that the user should actively communicate with the manufacturer in model selection and commissioning to jointly solve the problem and ensure the normal use of the oil cylinder.