Oil cylinder manufacturer There are many ways to inspect raw materials to ensure the quality and compliance of raw materials.
Here are some common methods:
1. Appearance inspection:
Appearance inspection is one of the common raw material inspection methods.
The quality of raw materials is evaluated by visual observation of their appearance, including color, shape, surface quality, etc.
Visual inspection can help determine whether the raw materials have obvious defects, flaws or contamination.
2. Dimensional inspection:
Dimensional inspection refers to the measurement and judgment of the size, dimensional deviation and shape of raw materials to evaluate their compliance with the design requirements.
Dimension inspection can be carried out through measuring tools such as micrometer and micrometer to ensure the accuracy and consistency of raw material dimensions.
3. Chemical composition analysis:
In some specific industrial fields, such as metal materials, plastics, etc., chemical composition analysis is a common raw material inspection method.
Detect the element composition of raw materials and check whether there are illegal or harmful substances through chemical analysis instruments such as spectrometer, X-ray fluorescence spectrometer, etc.
4. Physical performance test:
Physical property testing refers to testing and evaluating the mechanical, thermal, electrical and other properties of raw materials.
Common physical property tests include strength test, hardness test, thermal expansion coefficient test, resistance test, etc.
These tests can help to check whether the raw materials meet the specific process and use requirements.
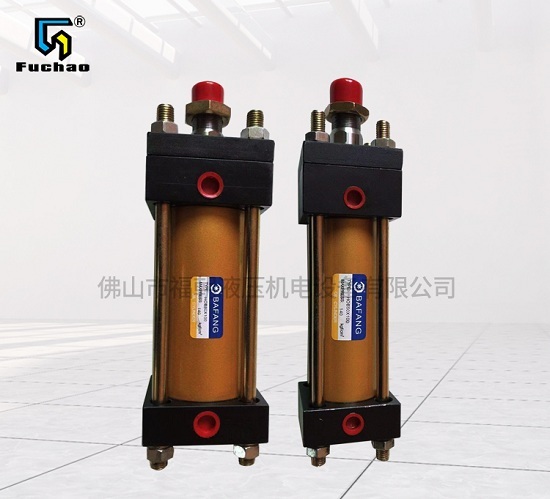
5. Microstructure observation:
Microstructure observation refers to the observation and analysis of the microstructure of raw materials through microscope and other equipment.
For example, the grain size and shape of metal materials and the phase distribution of plastic materials can be understood through microscopic observation.
This is helpful to judge the quality of raw materials in terms of purity, lattice structure, etc.
6. Package identification inspection:
Packaging identification inspection refers to the inspection and confirmation of packaging identification of raw materials.
The package identification usually includes the name, specification, batch number, production date, manufacturer and other information of raw materials.
The source of raw materials, quality certification and other information can be checked through the inspection of packaging marks.
7. Flammability and safety test:
For some flammable and explosive raw materials, it is necessary to conduct flammability and safety tests.
These tests include flash point test, autoignition temperature test, explosion limit range test, etc.
In addition, it is also necessary to check whether the raw materials comply with environmental protection and safety standards to avoid damage to human body and environment.
8. Moisture content test:
The moisture content test is conducted for some raw materials that are sensitive to moisture.
By measuring the moisture content of raw materials, we can judge whether they meet the process requirements and storage requirements.
The commonly used moisture content test methods include oven method, Karl Fischer method, etc.
In addition to the above common methods, the oil cylinder manufacturer can also adopt other more professional inspection methods according to the specific characteristics of raw materials and quality requirements. At the same time, oil cylinder manufacturers can also rely on third-party laboratories for testing and inspection to ensure the quality and compliance of raw materials.