Hydraulic pump Hydraulic system And hydraulic components generally adopt cylindrical slide valve structure, the valve core and valve body should be completely concentric in theory, so no matter how much pressure it works under, the force required to move the valve core only needs to overcome the viscous friction force, which should be very small in value (0.5~5N), but this is not the case in practice, especially in medium and high pressure systems, When the valve core stops moving for a period of time (generally about 5min), sometimes the resistance can be as high as several hundred Newtons, which makes it very difficult for the valve core to move. This is the so-called hydraulic clamping phenomenon of the slide valve.
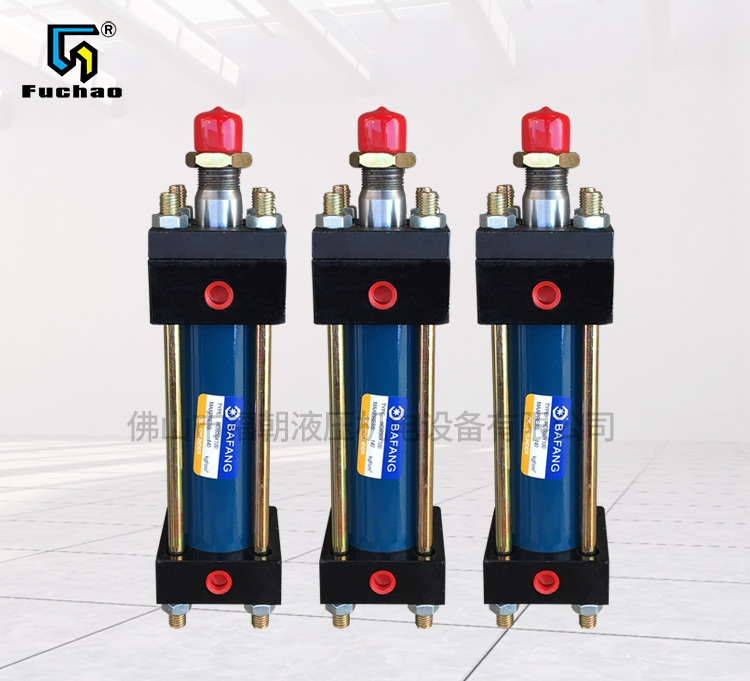
The hydraulic clamping in the hydraulic system increases the wear of the slide valve and reduces the service life of the hydraulic components. In the control system, the displacement of valve core usually uses electromagnet and spring with less force. The hydraulic clamping will make the generator act inefficiently or fail to act, resulting in adverse consequences for the system operation. For example, the valve core of the hydraulic valve works under continuous high pressure, and there is hysteresis or failure to reset after pressure relief. The electromagnetic reversing valve also has the phenomenon of slow reversing and even no reversing due to hydraulic clamping.