The valve is the control part in the pipeline fluid transmission system, which is used to change the channel section and the medium flow direction, and has the functions of diversion, cut-off, adjustment, throttling, check, diversion or overflow pressure relief.
The valves used for fluid control range from simple stop valves to various valves used in extremely complex automatic control systems, with a wide range of varieties and specifications. The nominal diameter of the valves ranges from very small instrument valves to industrial pipeline valves with a diameter of 10m. The valve can be used to control the flow of water, steam, oil, gas, mud, various corrosive media, liquid metal, radioactive fluid and other types of fluids. The working pressure of the valve can be from 1.3 х Ultra high pressure from 10MPa to 1000MPa, working temperature from - 269 ℃ to 1430 ℃. The valve can be controlled by various transmission modes, such as manual, electric, hydraulic, pneumatic, worm gear, electromagnetic, electromagnetic hydraulic, electric hydraulic, pneumatic hydraulic, spur gear, bevel gear, etc; Under the action of pressure, temperature or other forms of sensing signals, the valve can act according to the predetermined requirements, or simply open or close without relying on the sensing signals. The valve can lift, slide, swing or rotate the opening and closing parts by relying on the drive or automatic mechanism, thus changing the size of its flow channel area to achieve its control function.
I Purpose of valve
The valve is a pipeline accessory, which is a device used to change the channel section and medium flow direction, and control the movement of the conveyed medium. It has the functions of diversion, cut-off, adjustment, throttling, check, diversion or overflow pressure relief. Specifically, the valve has the following uses:
1.1 Block valves: connect or block the medium in each section of the pipeline. Such as gate valve, globe valve, ball valve, plug valve, diaphragm valve, butterfly valve, etc.
1.2 Regulating valves: regulate the flow and pressure of medium in the pipeline. Such as throttle valve, regulating valve, pressure reducing valve, safety valve, etc.
1.3 Diverter valves: change the flow direction of the medium in the pipeline to distribute, separate or mix the medium. Such as distribution valve, three-way plug valve, three-way or four-way ball valve, drain valve, etc.
The valve is the control part in the pipeline fluid transmission system, which is used to change the channel section and the medium flow direction, and has the functions of diversion, cut-off, adjustment, throttling, check, diversion or overflow pressure relief.
The valves used for fluid control range from simple stop valves to various valves used in extremely complex automatic control systems, with a wide range of varieties and specifications. The nominal diameter of the valves ranges from very small instrument valves to industrial pipeline valves with a diameter of 10m. The valve can be used to control the flow of water, steam, oil, gas, mud, various corrosive media, liquid metal, radioactive fluid and other types of fluids. The working pressure of the valve can be from 1.3 х Ultra high pressure from 10MPa to 1000MPa, working temperature from - 269 ℃ to 1430 ℃. The valve can be controlled by various transmission modes, such as manual, electric, hydraulic, pneumatic, worm gear, electromagnetic, electromagnetic hydraulic, electric hydraulic, pneumatic hydraulic, spur gear, bevel gear, etc; Under the action of pressure, temperature or other forms of sensing signals, the valve can act according to the predetermined requirements, or simply open or close without relying on the sensing signals. The valve can lift, slide, swing or rotate the opening and closing parts by relying on the drive or automatic mechanism, thus changing the size of its flow channel area to achieve its control function.
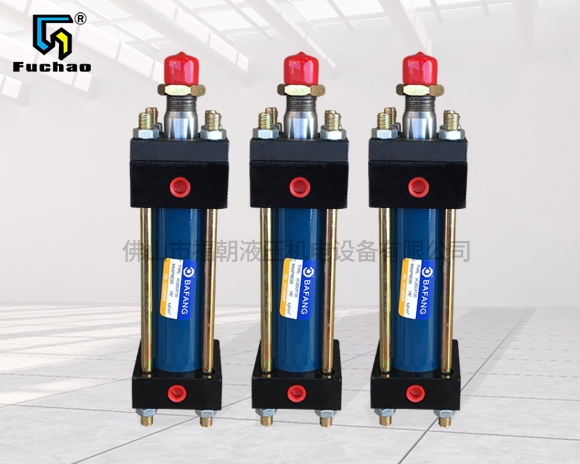
I Purpose of valve
The valve is a pipeline accessory, which is a device used to change the channel section and medium flow direction, and control the movement of the conveyed medium. It has the functions of diversion, cut-off, adjustment, throttling, check, diversion or overflow pressure relief. Specifically, the valve has the following uses:
1.1 Block valves: connect or block the medium in each section of the pipeline. Such as gate valve, globe valve, ball valve, plug valve, diaphragm valve, butterfly valve, etc.
1.2 Regulating valves: regulate the flow and pressure of medium in the pipeline. Such as throttle valve, regulating valve, pressure reducing valve, safety valve, etc.
1.3 Diverter valves: change the flow direction of the medium in the pipeline to distribute, separate or mix the medium. Such as distribution valve, three-way plug valve, three-way or four-way ball valve, drain valve, etc.
The valve is the control part in the pipeline fluid transmission system, which is used to change the channel section and the medium flow direction, and has the functions of diversion, cut-off, adjustment, throttling, check, diversion or overflow pressure relief.
The valves used for fluid control range from simple stop valves to various valves used in extremely complex automatic control systems, with a wide range of varieties and specifications. The nominal diameter of the valves ranges from very small instrument valves to industrial pipeline valves with a diameter of 10m. The valve can be used to control the flow of water, steam, oil, gas, mud, various corrosive media, liquid metal, radioactive fluid and other types of fluids. The working pressure of the valve can be from 1.3 х Ultra high pressure from 10MPa to 1000MPa, working temperature from - 269 ℃ to 1430 ℃. The valve can be controlled by various transmission modes, such as manual, electric, hydraulic, pneumatic, worm gear, electromagnetic, electromagnetic hydraulic, electric hydraulic, pneumatic hydraulic, spur gear, bevel gear, etc; Under the action of pressure, temperature or other forms of sensing signals, the valve can act according to the predetermined requirements, or simply open or close without relying on the sensing signals. The valve can lift, slide, swing or rotate the opening and closing parts by relying on the drive or automatic mechanism, thus changing the size of its flow channel area to achieve its control function.
I Purpose of valve
The valve is a pipeline accessory, which is a device used to change the channel section and medium flow direction, and control the movement of the conveyed medium. It has the functions of diversion, cut-off, adjustment, throttling, check, diversion or overflow pressure relief. Specifically, the valve has the following uses:
1.1 Block valves: connect or block the medium in each section of the pipeline. Such as gate valve, globe valve, ball valve, plug valve, diaphragm valve, butterfly valve, etc.
1.2 Regulating valves: regulate the flow and pressure of medium in the pipeline. Such as throttle valve, regulating valve, pressure reducing valve, safety valve, etc.
1.3 Diverter valves: change the flow direction of the medium in the pipeline to distribute, separate or mix the medium. Such as distribution valve, three-way plug valve, three-way or four-way ball valve, drain valve, etc.
The valve is the control part in the pipeline fluid transmission system, which is used to change the channel section and the medium flow direction, and has the functions of diversion, cut-off, adjustment, throttling, check, diversion or overflow pressure relief.
The valves used for fluid control range from simple stop valves to various valves used in extremely complex automatic control systems, with a wide range of varieties and specifications. The nominal diameter of the valves ranges from very small instrument valves to industrial pipeline valves with a diameter of 10m. The valve can be used to control the flow of water, steam, oil, gas, mud, various corrosive media, liquid metal, radioactive fluid and other types of fluids. The working pressure of the valve can be from 1.3 х Ultra high pressure from 10MPa to 1000MPa, working temperature from - 269 ℃ to 1430 ℃. The valve can be controlled by various transmission modes, such as manual, electric, hydraulic, pneumatic, worm gear, electromagnetic, electromagnetic hydraulic, electric hydraulic, pneumatic hydraulic, spur gear, bevel gear, etc; Under the action of pressure, temperature or other forms of sensing signals, the valve can act according to the predetermined requirements, or simply open or close without relying on the sensing signals. The valve can lift, slide, swing or rotate the opening and closing parts by relying on the drive or automatic mechanism, thus changing the size of its flow channel area to achieve its control function.
1. Purpose of valve
The valve is a pipeline accessory, which is a device used to change the channel section and medium flow direction, and control the movement of the conveyed medium. It has the functions of diversion, cut-off, adjustment, throttling, check, diversion or overflow pressure relief. Specifically, the valve has the following uses:
1.1 Block valves: connect or block the medium in each section of the pipeline. Such as gate valve, globe valve, ball valve, plug valve, diaphragm valve, butterfly valve, etc.
1.2 Regulating valves: regulate the flow and pressure of medium in the pipeline. Such as throttle valve, regulating valve, pressure reducing valve, safety valve, etc.
1.3 Diverter valves: change the flow direction of the medium in the pipeline to distribute, separate or mix the medium. Such as distribution valve, three-way plug valve, three-way or four-way ball valve, drain valve, etc.
2. Classification of valves
There are many types of valves. With the continuous improvement of the process flow and performance of various complete sets of equipment, the types of valves are still increasing, but in general, they can be divided into two categories:
2.1 Automatic valve
The valve operates by itself depending on the capacity of the medium (liquid, gas, steam, etc.). Such as safety valve, check valve, pressure reducing valve, drain valve, hydraulic control valve, emergency shut-off valve, exhaust valve, etc.
2.2 Drive valve
Valves operated by manual, electric, hydraulic and pneumatic means. Such as gate valve, globe valve, throttle valve, butterfly valve, ball valve, balance valve, plunger valve, plug valve, etc. The valve relies on an automatic or driving mechanism to make the hoist move up and down, slip, swing or rotate, thus changing the size of its flow channel area to achieve its control function.