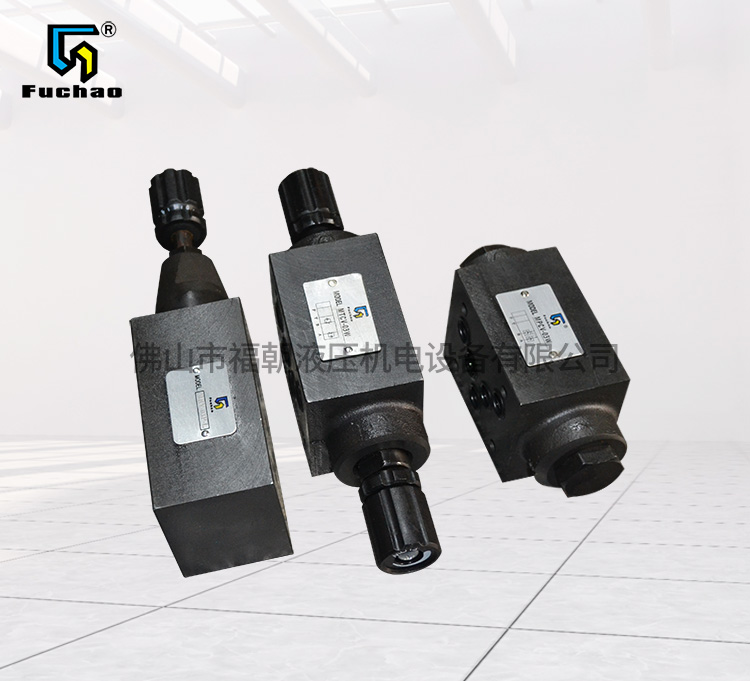
Hydraulic cylinder manufacturer Main factors affecting the sealing performance of hydraulic valves in
The main factor of sealing element damage is impurities in the working fluid. These impurities grind between the sealing elements, causing the valve to leak. Therefore, foreign countries have proposed that hydraulic components of corresponding grades should use filters of corresponding accuracy. They believe that the life of 5 μ M oil pump sealing element can be 10 times longer than that of 10 μ M oil pump sealing element if the filter with filtering accuracy of 3/μ M is used.
However, the working environment of hydraulic support valve is very bad. At the coal mining face, the total length of oil pipes is more than 1000 meters, there are more than 4000 joints and sockets, and there are no special dust prevention facilities for the fluid tank. There are a lot of floating impurities in the emulsion, and there are more coal dust, rock particles and iron chips left at the bottom of the column cylinder and the valve chamber. As the liquid inlet valve core and valve seat are opened and closed frequently, the liquid flow rate is high, and the seal will soon become invalid. Practice proves that the support is reduced Hydraulic system It is very difficult to pollute the impurities of the liquid. Someone once envisaged that the high-pressure filter should be used in the emulsion pump station, and a small filter should be added at the inlet of each support. However, it was quickly blocked in the work, forming a cutoff.